I arrived to check on a contractor’s progress on a tree removal and was drawn immediately to what appeared to be an improvised mechanical advantage system (for tree pulling) laying on the ground beside a felled spar consisting of a collection of climbing equipment, and some gear that could easily be confused as rigging or climbing equipment. A friction saver used as an anchor, a climbing rope reeved through a couple of hitch climber pulleys, a rigging block, two hitch cords, etc. The site supervisor assured me that they didn’t have to pull very hard to get the tree over (for what it’s worth). I couldn’t decide what was the best way to address my concerns because my gut was telling me that what I observed had deeper roots than the decisions of one tree worker. The problem? Climbing components that are configured for rigging tasks without a second thought, and with no consideration of where those components might end up next.
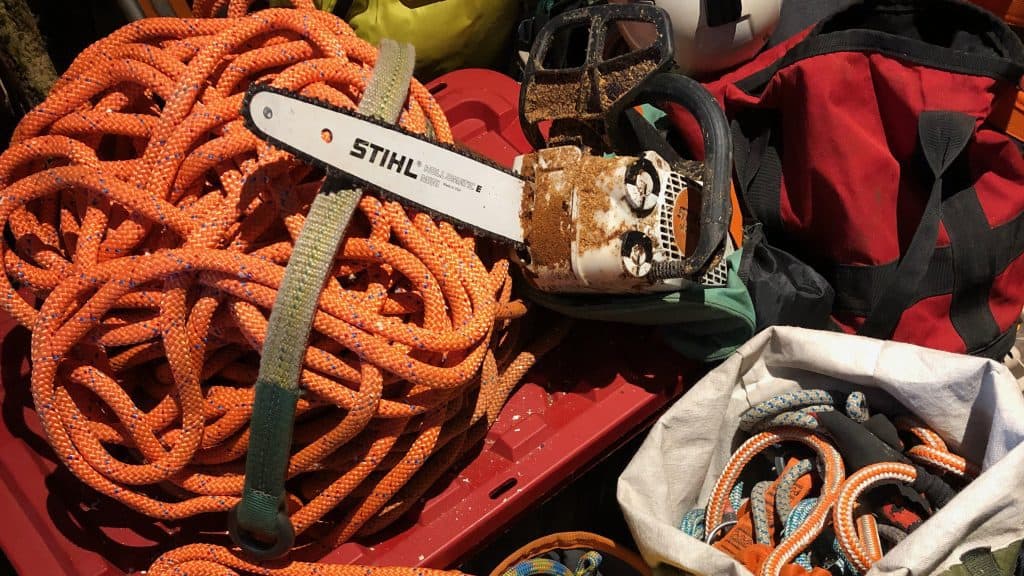
The source(s) of the problem is complex of course, combining:
- - A product development curve that has been fast moving and driven by a relatively small group of highly technical gearheads, and competition climbers.
- - Manufacturer product training programs that consist of a single international manufacturer representative presenting short sessions at major conferences and at a handful of workshops world-wide.
- - Introduction to products from your buddy that knows lots about gear, YouTube, or worse.
- - An inherent skepticism about gear cost versus benefits by supervisors or owners (that may ormay not be familiar with the gear being requested) or a negative perception of how gearpurchases might change work productivity.
- - A reluctance by climbers to spend money on gear due to the high cost or because the productsthey know are no longer produced.
- - Rushed apprenticeship periods or an inability to pair apprentices to mentors.
- - Supervision used rarely and reactively, rather than frequently and proactively.
- - A reluctance by supervisors or owners to spend money on gear due to past experiences ofequipment abuse, misuse, non-use, or loss.
- - An insistence by experienced workers that learned in gear-restrictive environments to passsimilar expectations along to new workers
- - A lack of understanding of how damage occurs to life supporting equipment
- - Casual attitudes toward risk to self and others
- - Omitted equipment incidents or close call accounts for fear of reprisal
- - Company provided climbing equipment programs that reassign used items (as personnel comeand go) without effectively logging entry of service, inspections, or reporting potential eventswhere Safe Working Loads/Working Load Limits have been exceeded.
- - The need to do physical work, with knowledge of tools that reduce physical and mentaldemands on a worker or workers.
Today’s fit-for-purpose tree climbing equipment is exceptionally well-built in terms of durability, wear indicators, and safety margins. Cases of equipment failure are less commonly seen in incident statistics, but less common does not mean uncommon. Three of my colleagues have fallen on account of equipment failure – one of whom did not survive. Many experienced climbers that keep themselves current on PPE inspection have direct experience removing gear from another climber that was down to its literal last threads. These are not gear problems, but gear-user problems (in most cases).
What do we do about it? The first step is examining your own workplace for conditions like those I’ve just bullet pointed. You could start by picking any tree truck at your workplace and pulling loose gear off it for examination. Tree trucks that have loose, unassigned climbing equipment such as climbing ropes, friction savers, carabiners or micropulleys indicates that there may be a problem. Knowing what you do, do you feel comfortable using those mysterious items based on a visual inspection alone, and is it reasonable to reassign that gear with origins or service history unknown? This is one of the main reasons why I buy my own gear, why I don’t loan my gear unless I am directly participating in the operation, and why I do my absolute best to account for each item after every use and ensure each piece of gear goes to its happy home when work is done. Remembering all the gear you have and when it entered service is no easy feat. Having all your gear recorded on an inventory makes for easy inspections.
The harder tasks won’t be solved in the short term and require those of us in positions of mentoring to think carefully about the values and lessons we’re sharing. If you find yourself frustrated by new equipment entering the workplace or how those tools might change how tasks are completed, a bit of money to secure time with professional industry trainers/product experts can help the entire crew learn in a safe setting improving familiarity, competency and productivity all at once across the workplace. If you find yourself deeply skeptical on the benefits of the latest tech to hit the tree gear showroom, you’re not alone. If you’re determined to use modern tools as a workplace cultural incompatibility indicator, then you most definitely have your work cut out for you on recruiting and retraining. If you swear it’s the last, last, last time you’ll ever buy an expensive item for a climber because it’s been lost yet again, you could consider talking to some of your colleagues in the tree business for other ideas to encourage gear appreciation and accountability. Restricting climbers from the gear they like to use or need to use will have compounding effects starting with diminishing morale for the climber and eventually their coworkers (precursors to flight risk, property damage risk, or injury risk). Yes, there are abusers, but amnesty is in unnecessarily short supply considering what those tools deliver in productivity, ergonomics and safety.